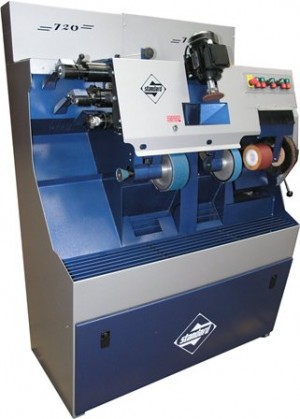
he preparation and supply of shoe repair equipment has occupied the attentions of Standard and formerly Whitfield Wylie for the almost mind-boggling period of three centuries! Admittedly 1892 – 2013 is “only” 121 years, but still, it encompasses 3 centuries!
In that time the design of the machinery has changed remarkably little, due in no small part to the equipment still being needed to do much the same job. A new 720 finisher supplied today, could, with only a small amount of consideration, we believe be used by a shoe repairer working during the latter stages of Queen Victoria’s reign. We are content with this. Our machinery, to coin a phrase, “does what it says on the tin!” There is often value in simplicity.
Most of our European cousins, by and large take a different, if equally valid approach when it comes to building shoe repair equipment. Their websites are filled with machinery, laden with ever more innovative add-ons and gizmos. Touch panel this. Auto activation that. Off-board the other. There are some amazing machines out there. Assuming you have very deep pockets. A very large premises. And three phase power. Oh, and like the colour grey!
Standard have found with much of this equipment is when it works well, it is very impressive. However, when there are issues often a lot of very expensive electronics and entire control panels can need replacing. Assuming a service engineer can be arranged, of course.
Although Standard’s equipment is invariably simpler than the comparable kit from Europe (where an appreciable percentage of repairers also work as podiatrists, requiring additional tooling and operations) it does not mean they are resting on their laurels. Over the past year or so we have engaged in a number of important developments to keep production and operating costs down and improve the lot of the humble shoe repairer. Little things. Useful things.
Such as fitting our range of flash activators with an automatic shut off so the unit can’t accidentally be left on for hours on end, burning power, inflating energy bills, and depleting the life of the tubes.
Using lighter, advanced materials in our finishers, which can reduce the initial power surge in starting the scouring band motor for instance, reducing energy used and ultimately, cost. This, in addition, puts less strain on the motors which will give them longer life over time.
We have also been tweaking the design of their press units, strengthening the framework, whilst reducing the overall weight, which, if nothing else, makes the machinery slightly easier for our delivery people to move! Today’s press units are fitted with quiet, efficient compressors, and better, more efficient cylinders. We have regulators on the air lines to reduce the air required for their operation, which, again improves the operating quality and the life-expectancy of the machinery, as well as being energy saving.
Obviously all these developments need the back-up of good housekeeping, such as ensuring air leaks are kept to a minimum and the oil is regularly topped-up.
We continue to look at all aspects of their machinery in order to improve reliability, performance and energy usage, to ensure their position as the Number One Machinery supplier in Europe.